What is Non-Destructive Testing (NDT)? Definition, Methods, and Applications
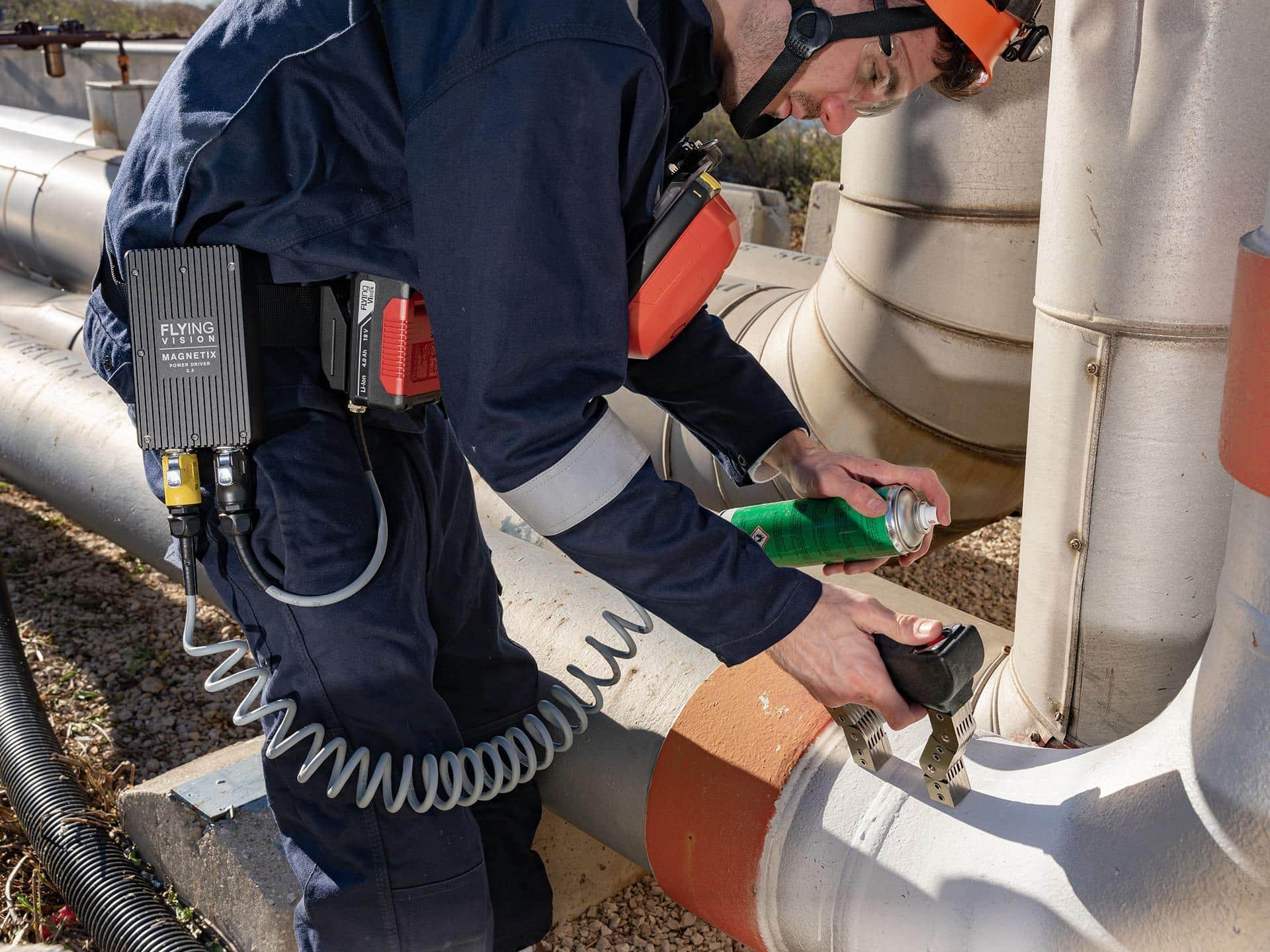
Non-destructive testing (NDT) is a set of methods and techniques that allow you to assess and verify the integrity of your materials or structures throughout their life without altering them. Performing NDT checking is essential to ensure the safety and robustness of your products or to quickly detect potential defects.
To successfully conduct a non-destructive inspection, it is crucial, depending on your industry needs, to choose the right method and tools. Radiography, ultrasonics, and magnetic particle testing – each NDT method will be more or less suited to guarantee a quality check.
Let Flyingvision guides you through the concept, methods, and application of NDT and use the best technical and robotic products to verify the integrity of your structures and installations throughout their life:
What is non-destructive testing?
Non-destructive testing (NDT) encompasses all methods that allow the inspection of the health and integrity of materials, installations, and infrastructures in various industries (energy, petrochemical, steel, etc.). NDT aims to highlight potential defects in the elements being tested without degrading or compromising their future use.
Also called non-destructive examination (NDE) or non-destructive inspection (NDI), these non-destructive tests are essential elements of quality control, providing information about the integrity of the material or infrastructure at various stages of its life, whether during production, use, maintenance, or dismantling. The information provided by NDT concerns, notably, the availability, the compliance, or the safe use of the product for its intended purpose.
Non-destructive testing allows inspectors to check the health of installations, to identify existing defects to bring them up to standard, and, thereby to ensure their quality, safety, and durability.
What is the difference between non-destructive testing and destructive testing?
Non-destructive testing is used to collect data about an object, a material or an installation without altering it, whereas destructive testing, or DT, requires the alteration, i.e, the destruction of the material, when collecting the data.
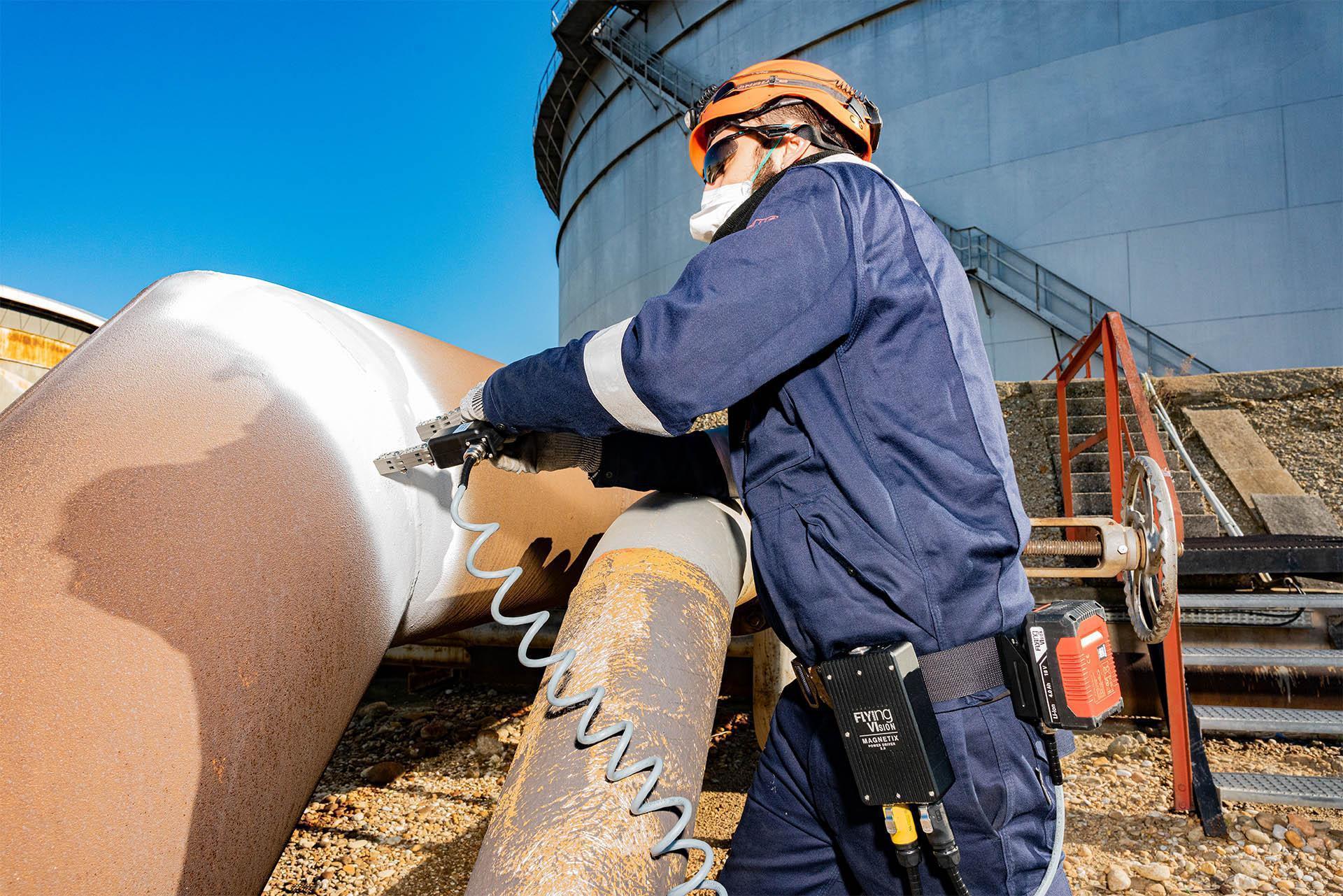
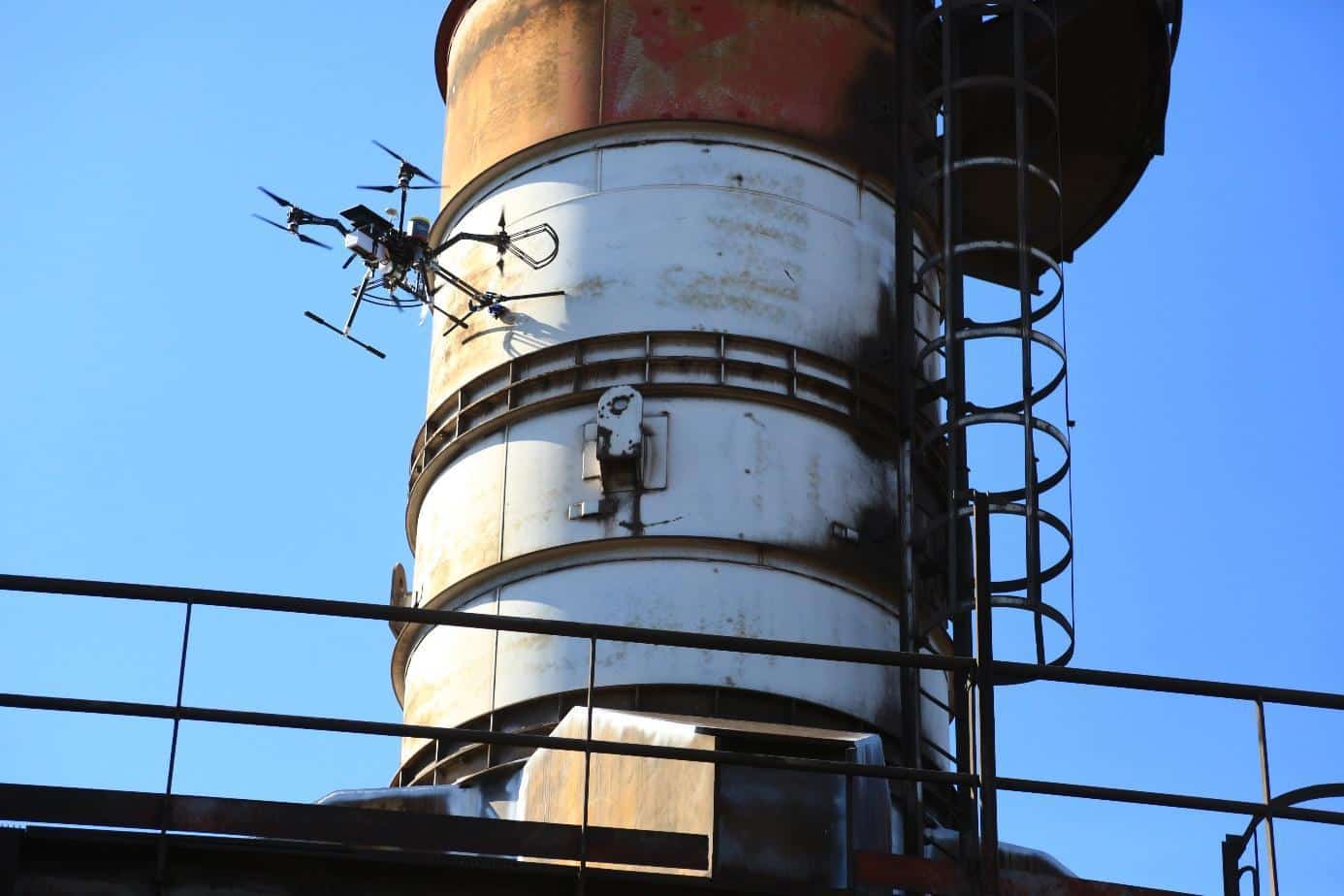
Why perform non-destructive testing?
The goal of non-destructive testing is to highlight any defects or risks that might impair the integrity of a given product relative to its intended use. Ensuring this quality control guarantees better risk management in case of danger and ensures greater safety for the workers and equipment.
Moreover, the nature of NDT allows the evaluation of the quality of a product, a structure, or an installation without degrading or destroying them and without even needing to move them. This ease of testing thus allows the industry conducting the tests to save costs.
As such, or companies, NDT possesses many benefits:
Saving money: By allowing the examination of the material or object being without harm, the company will save money and resources.
Safety: All NDT methods are harmless (except for radiographic testing).
Efficiency: Non-destructive testing is very efficient, allowing for a thorough and relatively quick evaluation of assets on-site.
Accuracy: NDT inspections, with the right tools, are very accurate, reliable, and predictable.
While this approach can be regulatory, as in the case of non-destructive examinations for ski lifts or pressure vessels, it is mostly voluntary, aligning with the quality policy of the concerned industries.
Which Industries Are Concerned with NDT testing?
What are the NDT codes and standards?
To ensure proper safety when conducting NDT testing, most countries have laws requiring companies to adhere to specific inspection codes and standards. Among the various NDT codes and standards, we have:
The ASNT: American Society For Nondestructive Testing.
The CSA Group: Canadian Standards Association.
The CEN: European Committee for Standardization.
The BSI: British Standards Institution.
The BINDT: British Institute of Non-Destructive Testing.
The EEMUA: The Engineering Equipment and Materials Users Association.
The COFREND: French Committee for Non-destructive Testing Studies.
The AFNOR: French Association for Non-Destructive Testing.
The COFRAC: French Accreditation Committee.
The DGZfP: German Society for Non-Destructive Testing.
Some of the European NDT standards are:
EN 473: Qualification and certification of NDT personnel.
EN ISO 9712: Non-destructive testing – Qualification and certification of NDT personnel.
EN ISO 13588: Non-destructive testing – Qualification and certification of NDT inspection agencies.
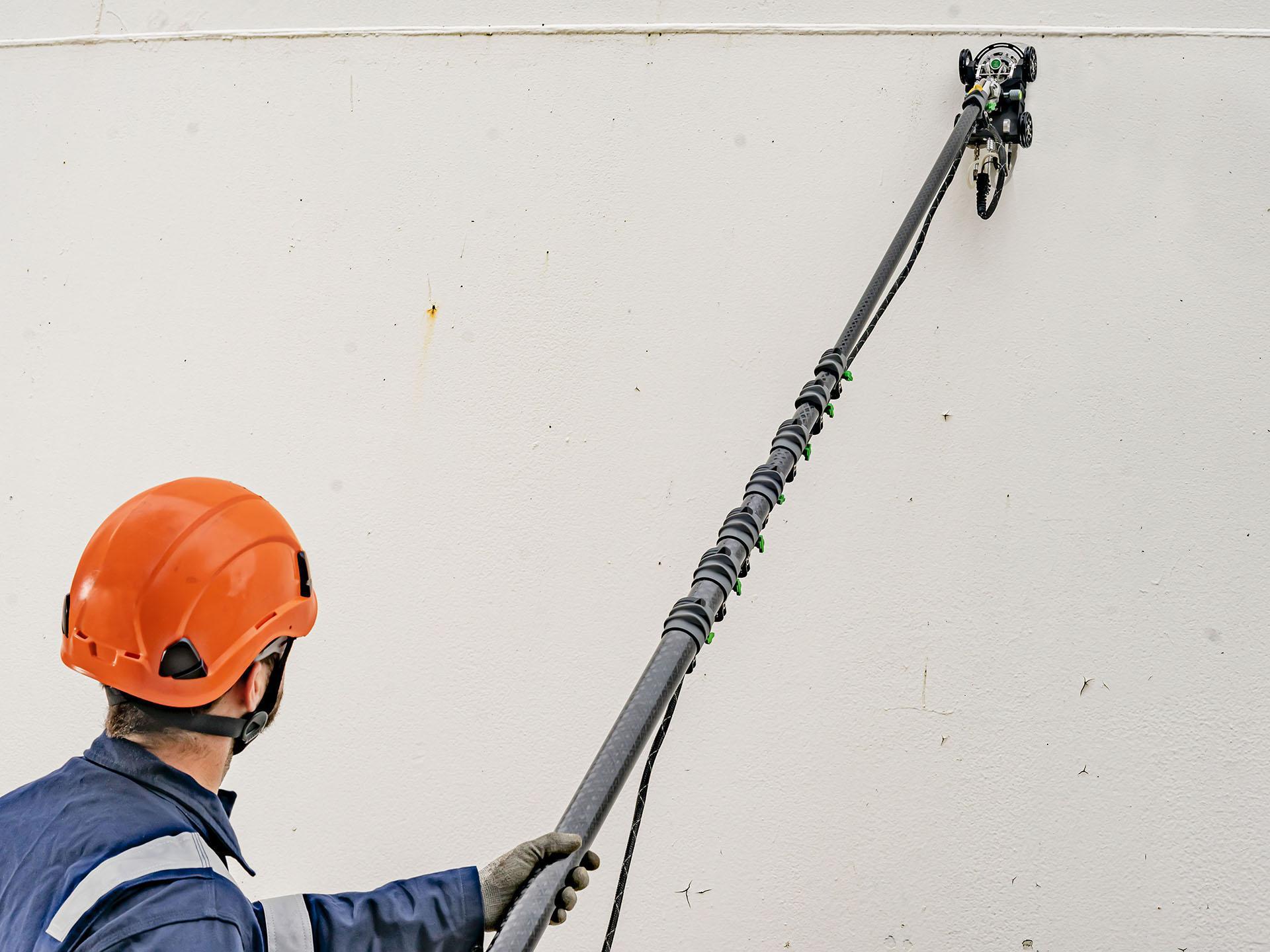
What Are the Different Methods of Non-Destructive Testing?
Nondestructive testing and evaluation consist of several methods, each offering the highest quality and reliability to meet specific needs. Among these non-destructive testing methods, we find:
Magnetic Particle Testing (MT): Magnetic particle inspection is an essential magnetic field method that detects surface defects (cracks, fissures, tears) on ferromagnetic elements.
Ultrasonic testing (UT): A method that analyses an ultrasonic wave propagated in the inspected piece. These waves will behave differently based on the surface discontinuities encountered. Although this NDT can be performed on most materials, the behaviour of projected sound waves will be influenced by the material’s structure.
Radiography (RT): A type of NDT inspection that reveals certain compactness defects in a product or in materials, or probes the heart of a piece. This method passes a gamma ray beam through the concerned element and irradiates a photographic film placed behind the inspected surface. Radiography can be performed on all types of materials.
Visual Inspection (VT): Visual testing encompasses all techniques using the visible light spectrum. It is the most basic method of NDT to examine a material or object without altering it.
Leak Testing (LT): Locates leaks and determines their significance in terms of flow or rate.
There are other types of NDT techniques, such as electromagnetic testing (ET), acoustic emission testing (AE), eddy current testing, ground penetrating radar (GPR), thermal/infrared testing (IRT), liquid penetrant testing (LPT), etc.
To meet all your specific non-destructive testing needs, Flyingvision offers innovative products for each method. We develop and manufacture a wide range of non-destructive inspection products for service provider companies in many industrial fields (energy, naval construction, steel, petrochemical).
What Potential Defects Are Sought in NDT?
Non-destructive testing helps identify three types of defects:
Non-compliance with specifications: Incorrect dimensional measurements, incorrect angles, incorrect surface condition, etc.
Internal defects: Porosities, blowholes, inclusions, non-penetrating cracks, thickness variations due to wear or corrosion, etc.
Surface defects: Cracks, holes, fissures, pits, etc.
In addition to detecting these defects, a non-destructive test will characterise and precisely size them to ensure the best compliance.
What Is the Scope of Application of Non-Destructive Testing?
Due to the importance of quality control, safety, and risk management, non-destructive testing has become essential in many industrial sectors, with an ever-expanding scope of applications.
Non-destructive inspection can be conducted at three distinct stages of a product or installation’s life cycle: before manufacturing, during manufacturing, and during use:
Before manufacturing: NDT can analyse a product and check its quality specifications against the bill specifications. At this stage, NDT testing helps detect defects and define their nature and dimensions.
During manufacturing: Non destructive examinations control processes, especially those automated and involving equipment installed on the production line. At this stage, NDT, having identified the defects, helps to spot and sort defective products.
During the use of the product or installation: Especially during maintenance or after detecting behavioural anomalies, non destructive testing plays an essential role. To ensure the highest reliability, NDT estimates the nature and dimensions of the damages as accurately as possible to determine their severity and potential harm.
Do you want to use the best tools and equipment for your non-destructive testing? Flyingvision is your trusted partner for high-performance and innovative NDT and evaluation solutions.