OUR SOLUTIONS FOR VACUUM BOX LEAK TESTING (NDT LT)
Are you seeking a reliable, quick, and long-lasting solution for leak testing your welded joints?
Flying Vision has developed an innovative range of vacuum boxes and vacuum pumps that meet most bubble leak testing requirements using vacuum chambers.
Can’t find the right solution for your setup? Looking for vacuum boxes for sale? Curious about vacuum box testing equipment prices?
Feel free to contact us for custom adaptations or bespoke development of our vacuum box systems.
Our product
Vacuum Box
VACUUM BOX BAV-7025
Ref : BAV-A100-001
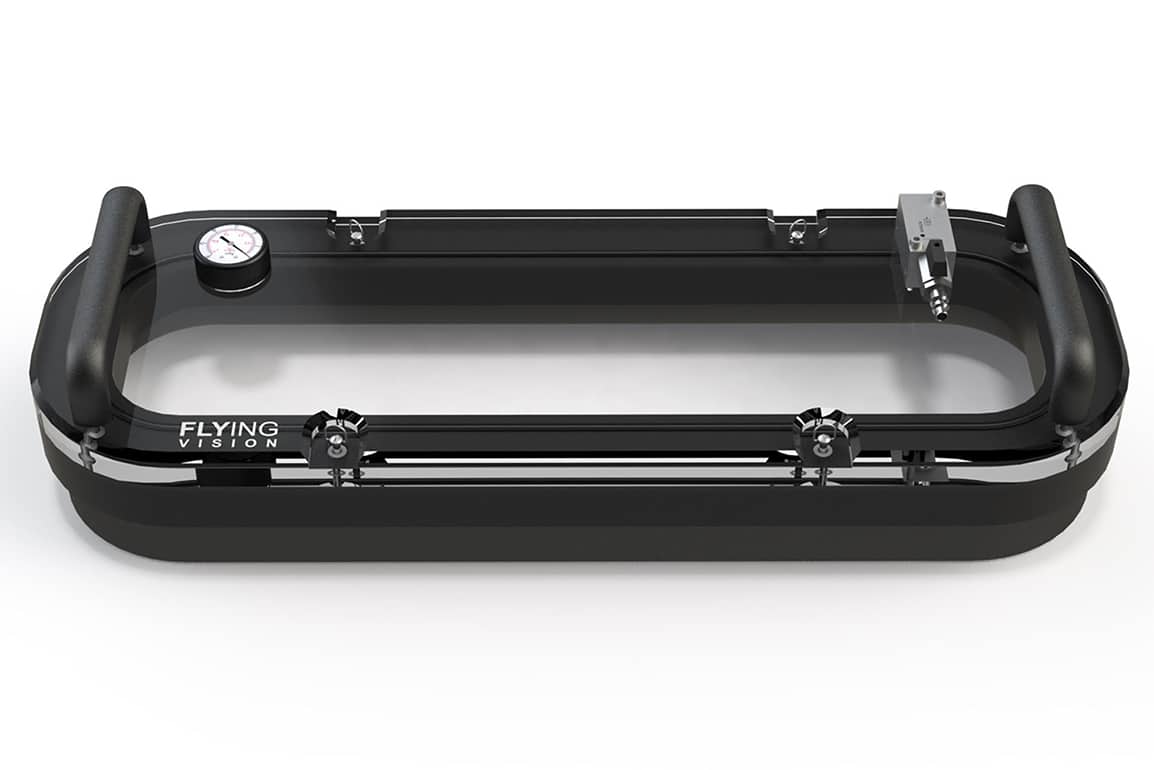
CONTROL CONFIGURATION
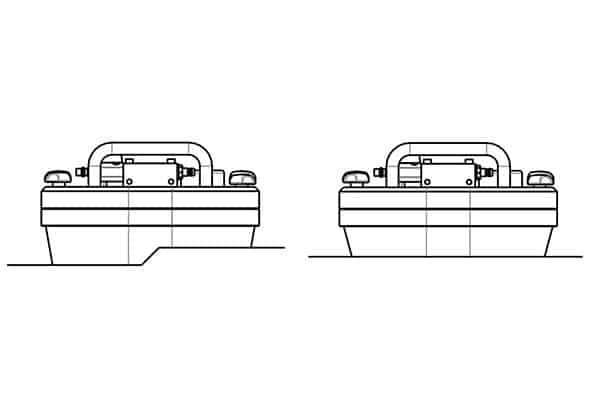
Vacuum box designed for leak testing on:
- Flat welds
- Lap joints, lap welds
- Internal or external circular welds depending on the curvature radius
VACUUM BOX BAV-4025
Ref : BAV-A200-001
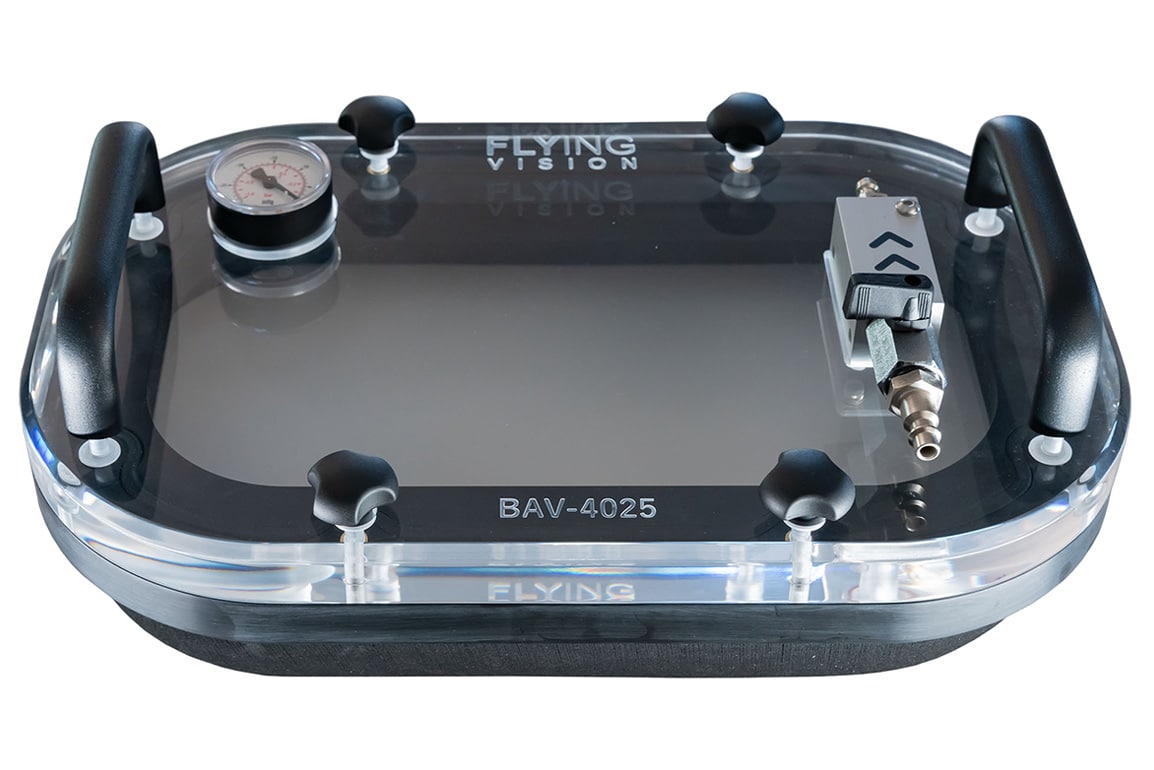
CONTROL CONFIGURATION
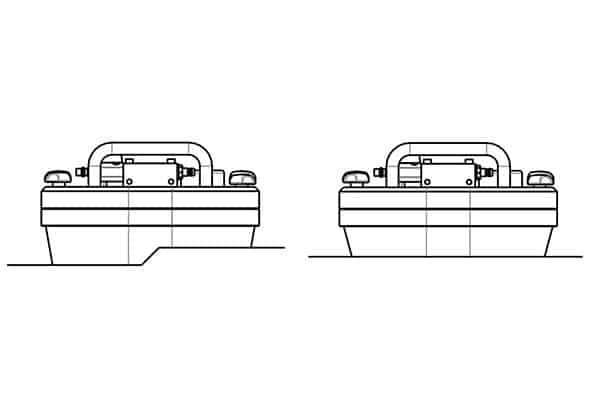
Vacuum box designed for leak testing on:
- Flat welds
- Lap joints, lap welds
- Internal or external circular welds depending on the curvature radius
VACUUM BOX BAV-4025A SERIES
Ref : BAV-A300-x
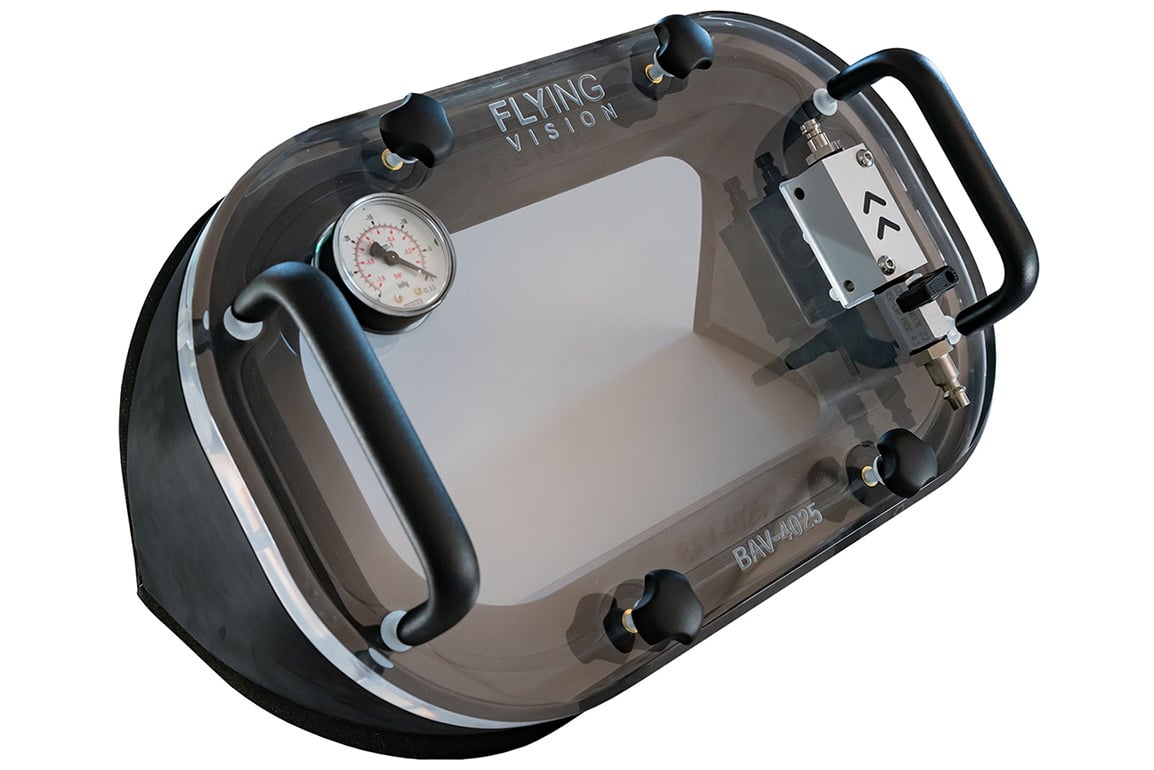
CONTROL CONFIGURATION
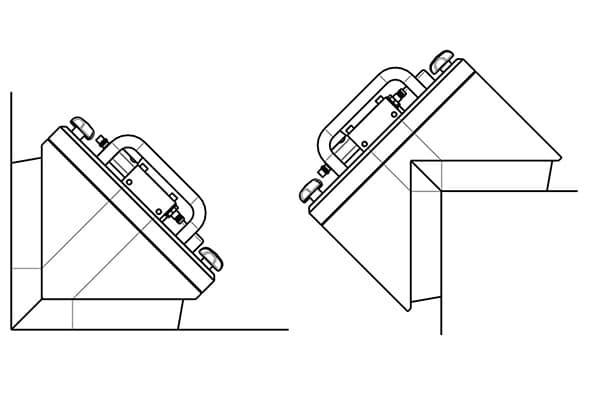
Series of vacuum box designed for leak testing on:
- Internal angle welds
- External angle welds
- Internal or external angle welds with a varying angle
VACUUM BOX BAV-40C
Ref : BAV-A400-001
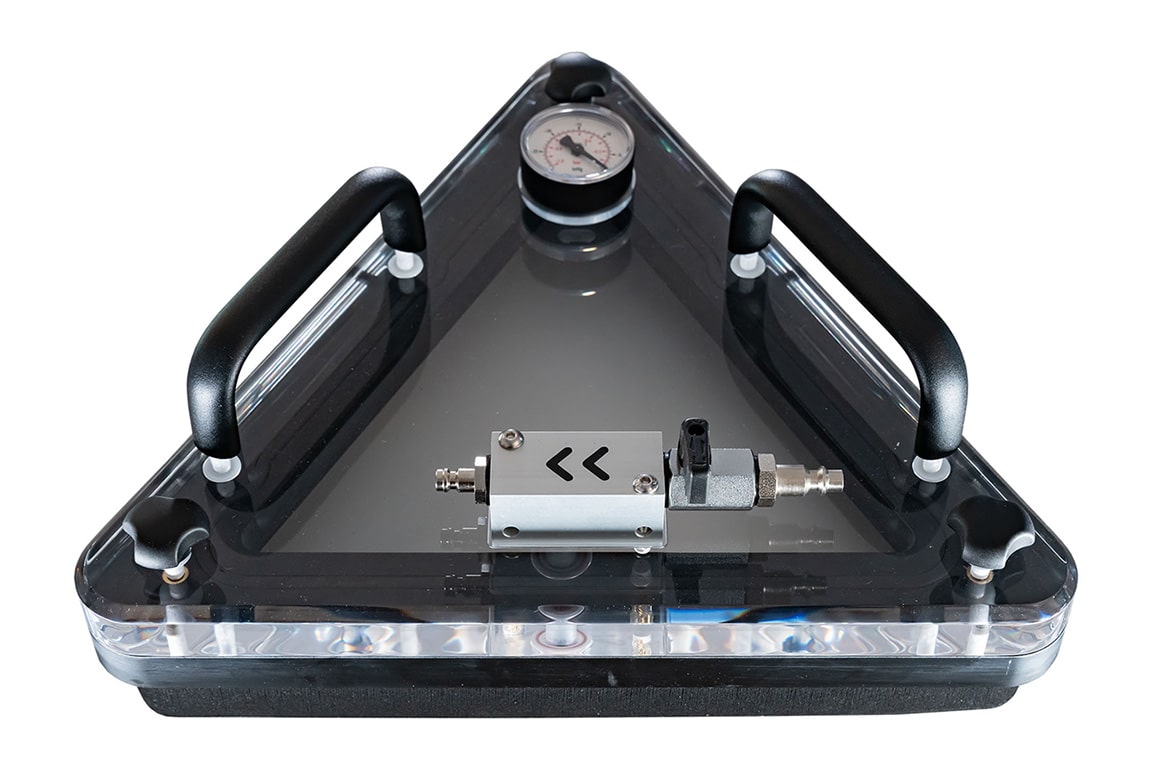
CONTROL CONFIGURATION
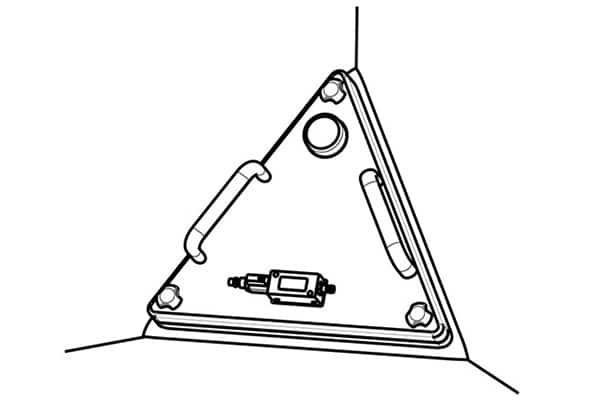
Series of vacuum boxes designed for leak testing on:
- Internal corner welds at 90°
- Internal corner welds where an isosceles plane is
- Present
Vacuum Pump
VACUUM PUMP
Ref : PAV-B8-xxx
110/120V or 220/240V Dry vacuum pump
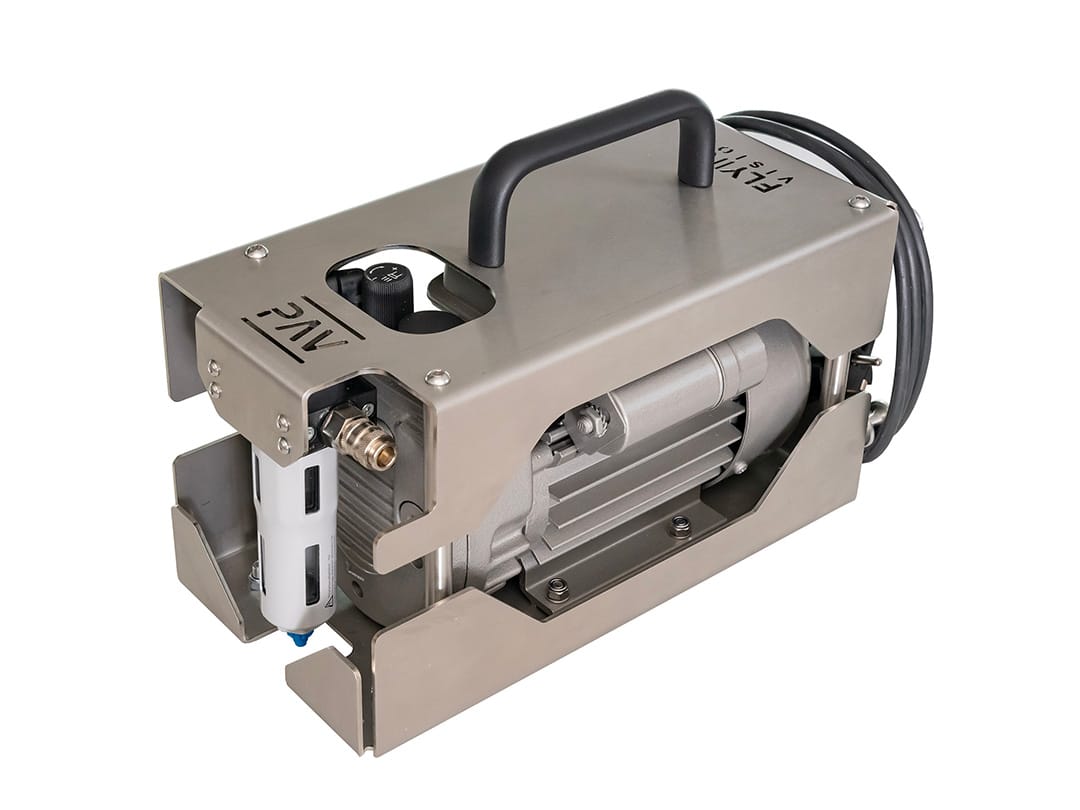
8 m³/h – 150mbar vacuum – Dry vacuum pump designed for most demanding field conditions.
It is the ideal solution for generating vacuum during your vacuum box leak testing operations.
Options and Accessories
silicone SPACERS KIT
Ref : BAV-090
For vacuum box inspections of lapwelds
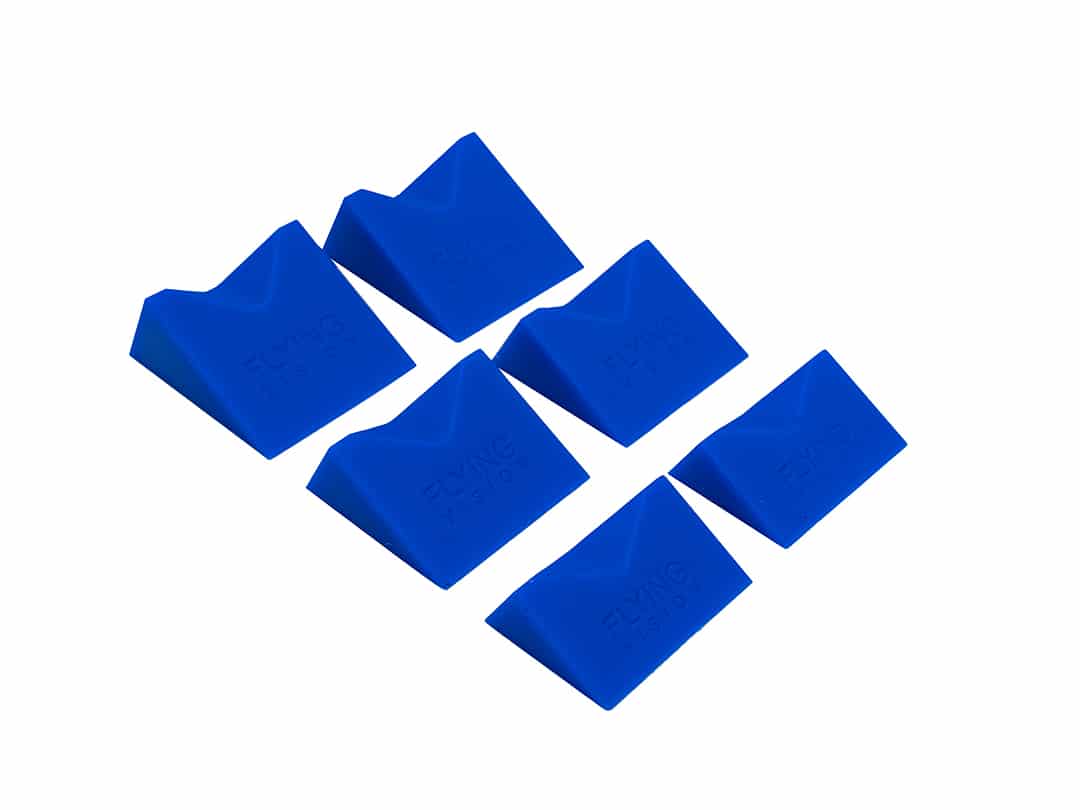
Innovative solution to perform vacuum box leak testing on lap weld joints up to 25 mm, depending on the vacuum box model selected.
LED LIGHTING
Ref : BAV-A050
Led lighting option for all BAV vacuum box series
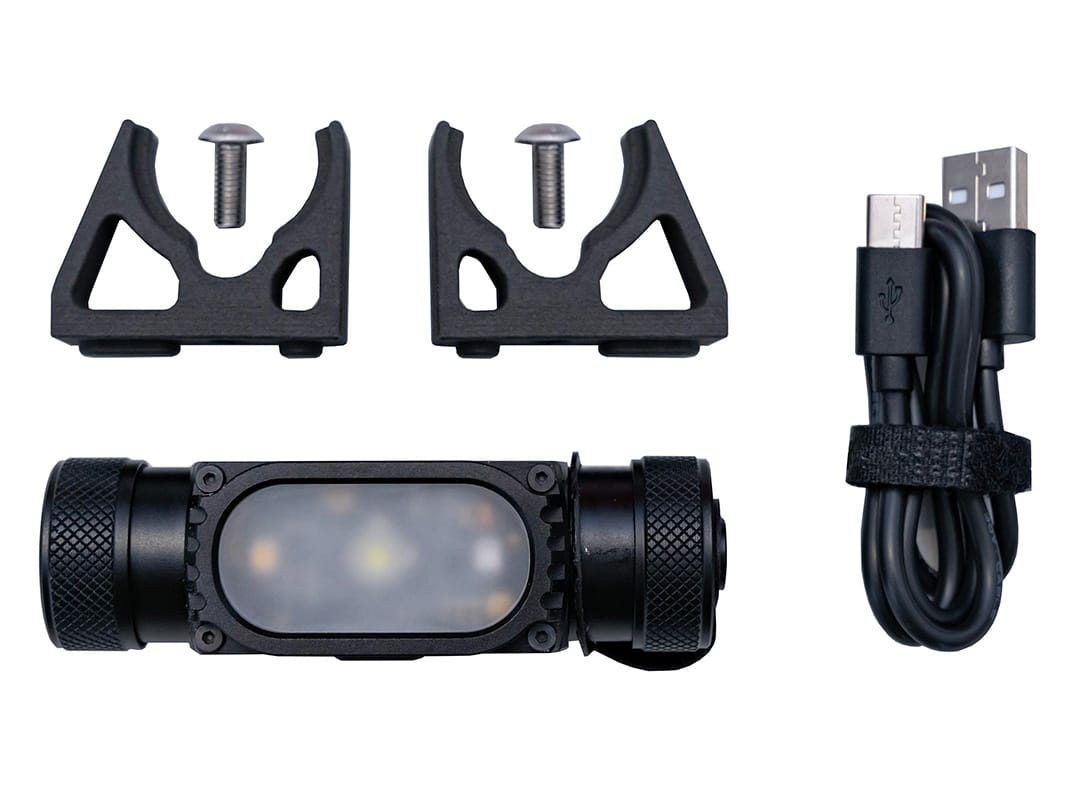
Removable, battery-powered LED lighting system designed for all BAV vacuum box series.
This accessory makes it easy to achieve the minimum required lighting level during your vacuum box leak inspections.
VACUUM PUMP HOSES
Hoses for the PAV-B8 series vacuum pumps
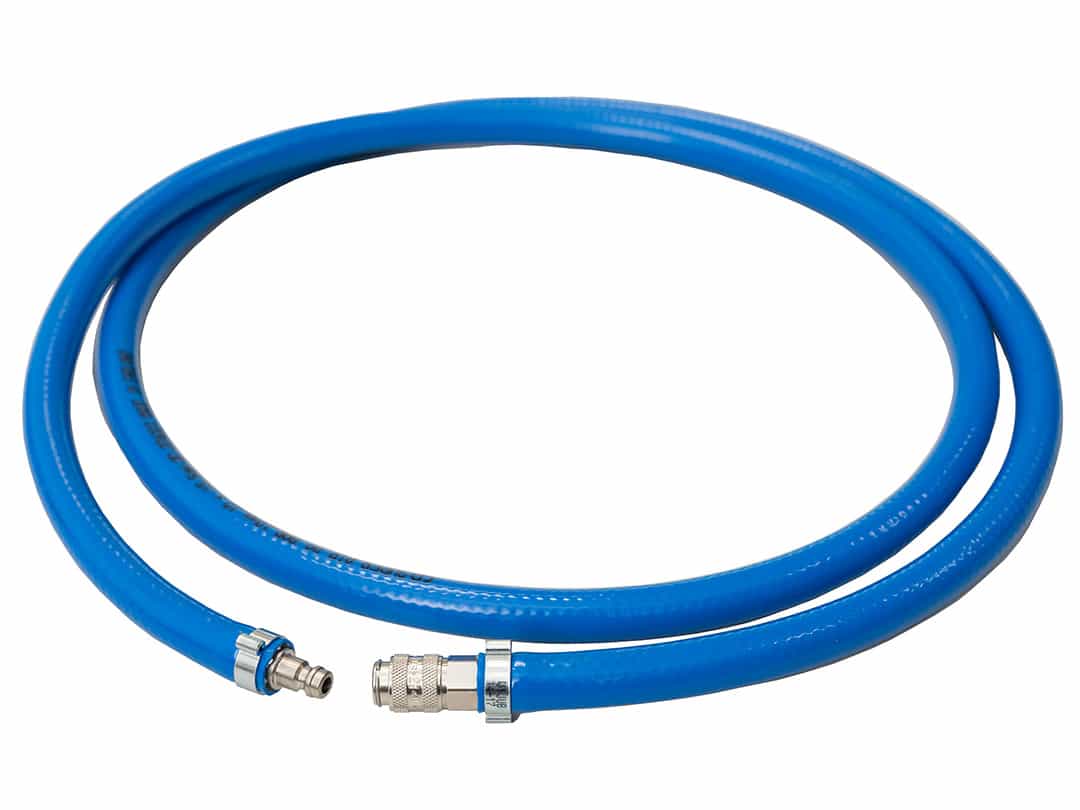
Extension hoses equipped with Rectus 21 male and female quick couplings, for connecting any BAV series vacuum box to your PAV-B8-XXX vacuum pump.
Vacuum box leak testing
Operating principle
Vacuum box testing is a non-destructive testing (NDT) method used to check the seal integrity of welded joints. This process utilizes a vacuum box, often made of Plexiglas, in conjunction with a vacuum system to create a pressure differential. A reactive agent, which generates bubbles, is applied to the surface under test.
Purpose of the bubble leak test
The main goal of this bubble leak testing method or vacuum box inspection is to identify leaks in systems that cannot be conventionally pressurized. In the event of a leak, the reactive agent creates bubbles, providing a visual indication of the leak.
Therefore, it is essential to maintain a clear reading of indications that the distance between the vacuum box’s window and the inspected surface be at least 1 to 2 cm.
Areas of application
- Vacuum box test for tanks / Storage tanks (vacuum box testing tank bottom or shell)
- Ship hulls
- Overlap, butt welds (vacuum box weld testing equipment)
- Roofing waterproofing sheets and membranes for flat or terrace roofs
- Any other surfaces (metallic or not) where a pressure gradient can be applied
General design of our industrial vacuum box
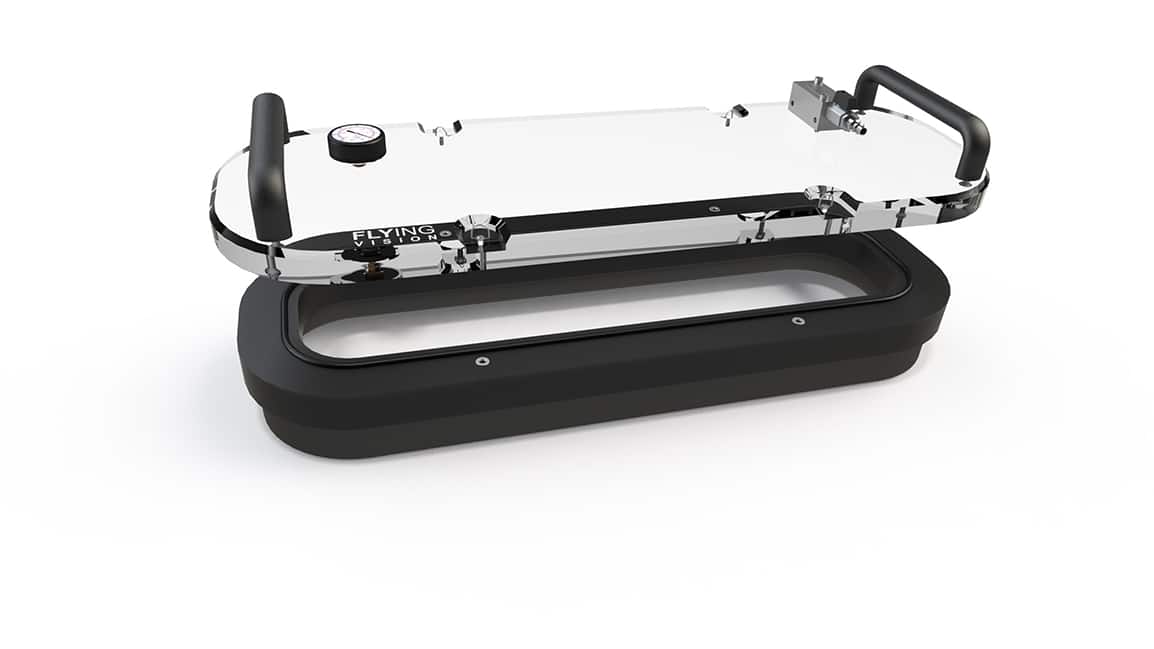
To address the issues of equipment maintainability (maintenance), versatility, and to ensure good readability of indications (height of the viewing window), we have developed a line of vacuum box with a completely innovative two-part design:
- The main body composed of handling grips, a pressure gauge, and an integrated hybrid vacuum system for optimal compactness.
- The base composed of foam tailored to the configuration of your inspection surface. This base primarily ensures a sufficient viewing window height for reliable inspections and allows for equipment longevity, as the foam base becomes an easily replaceable consumable.
Control Configurations
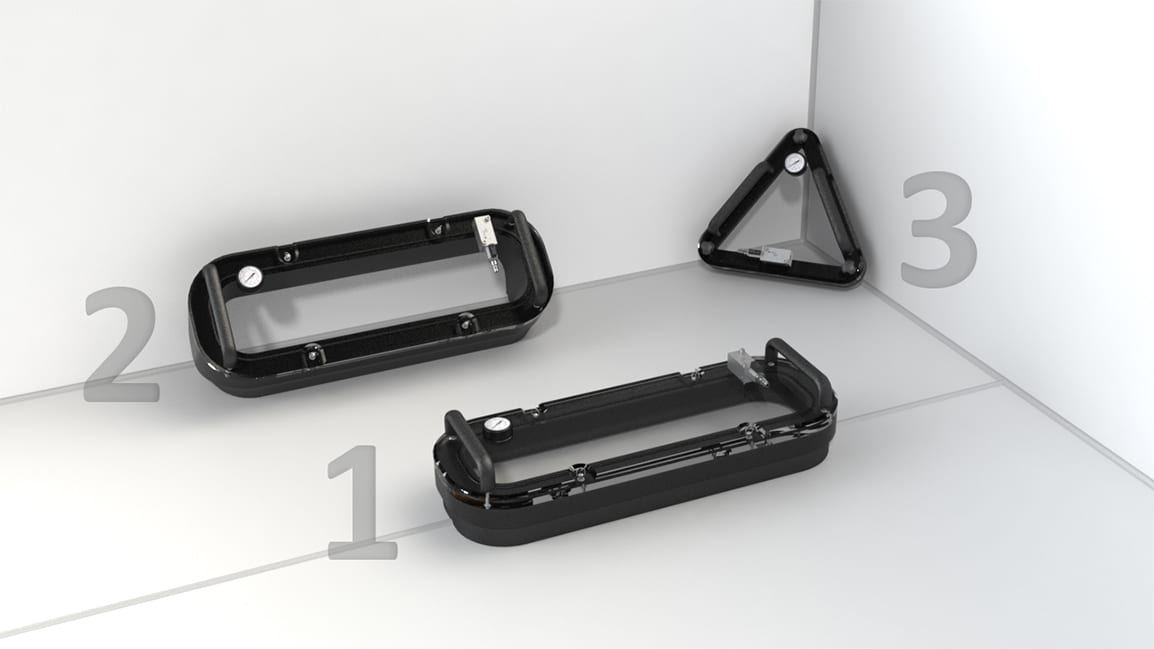
Our range of vacuum box testing equipment covers a wide array of inspection configurations:
- Flat welds, butt, overlap, fillet, with our flat-base vacuum box ndt (types BAV-7025 or BAV-4025)
- Internal right-angle welds with our internal corner vacuum box (types BAV-7025IA or BAV-4025IA)
- Internal corner welds with our triangular corner ndt vacuum box (type BAV-40IC)
It should be noted that the bases of our flat and internal right-angle vacuum box are interchangeable, allowing you to have just one vacuum box body and to choose the desired base configuration.
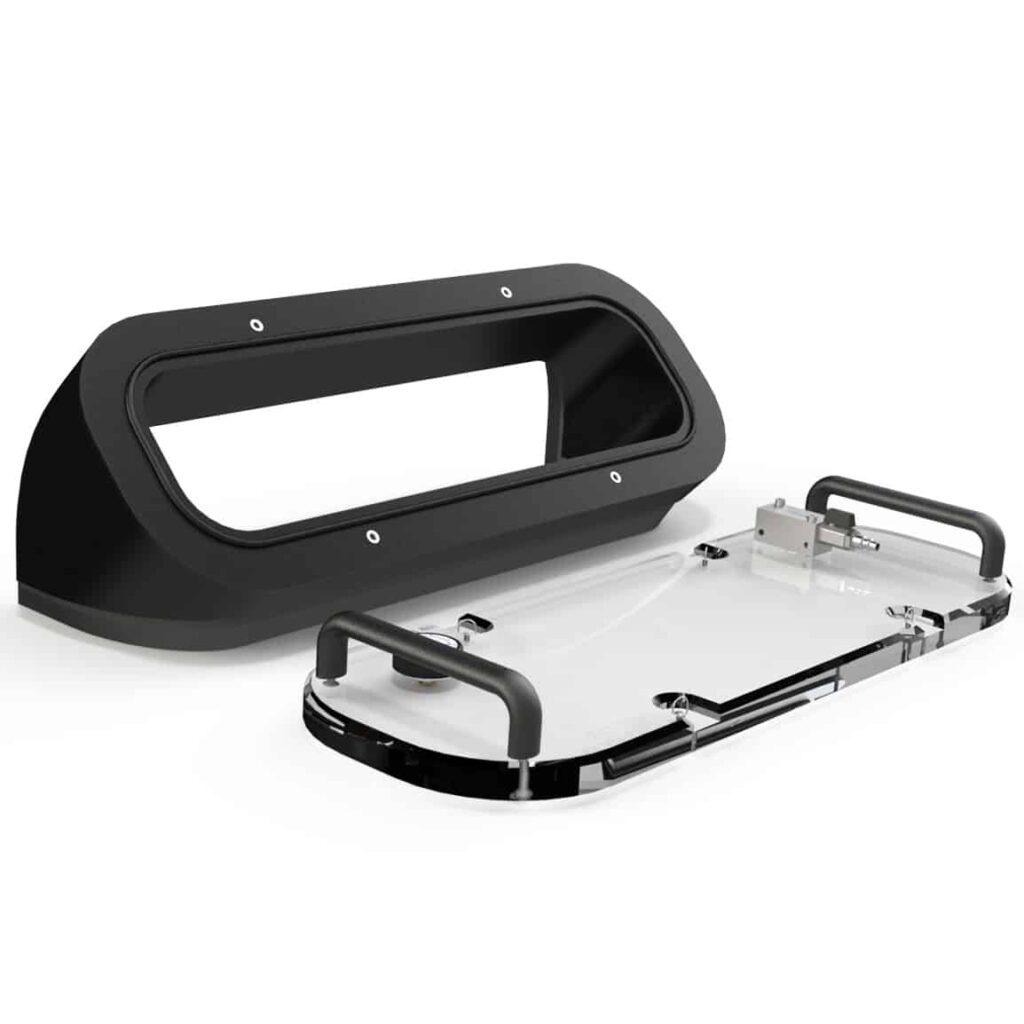
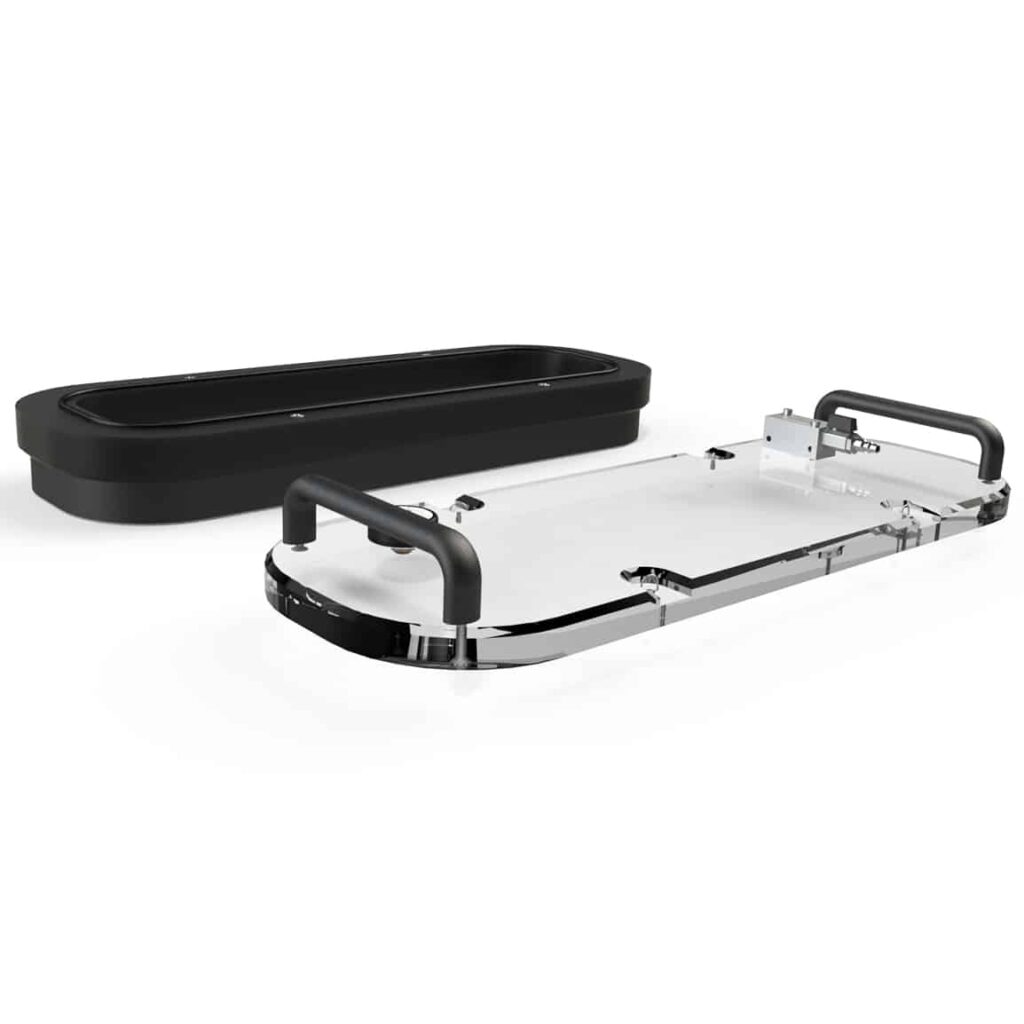
Vacuum Generation Capacity
The surfaces under inspection can be very heterogeneous depending on the application requiring this type of control. For instance, in the case of roofing or terrace roof leak testing, your surface will be smooth and regular with very little deformation, whereas in the case of a petrochemical industry storage tank, you may encounter irregular, granular, or even abrasive surfaces with significant excess thickness (especially in the case of fillet welds).
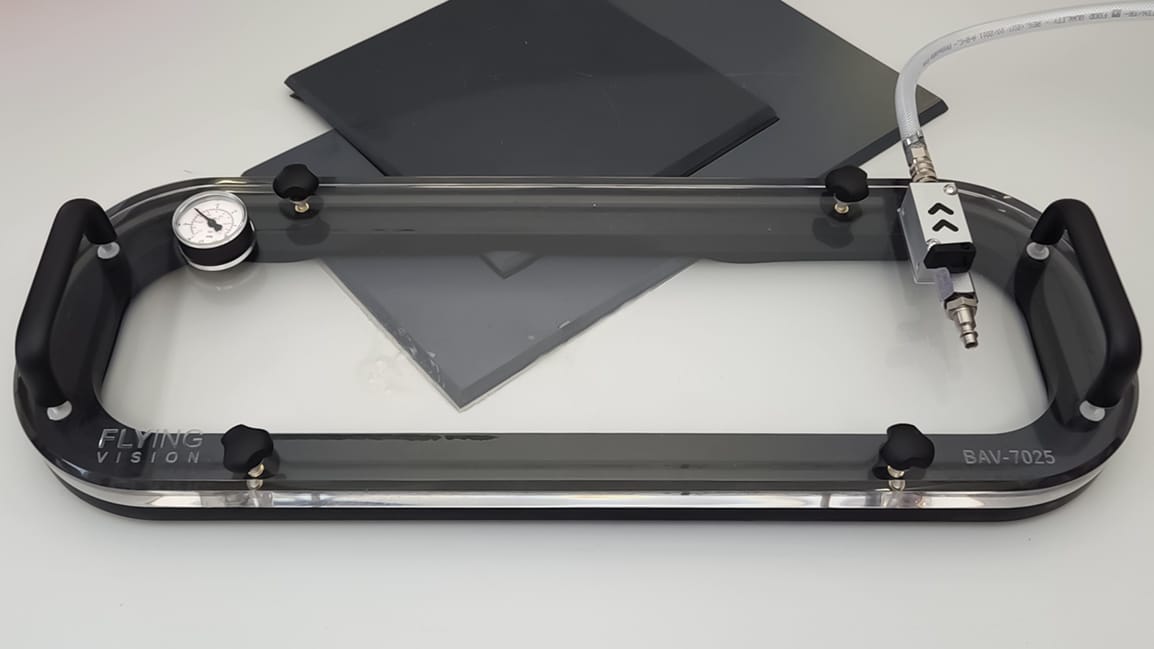
The success of the leak test depends directly on the foam’s ability to conform to the shape of the inspection surface; otherwise, a vacuum cannot be created.
To perfectly address these challenges, we have conducted extensive development work on our foams regarding their shape, material, manufacturing method, and adhesion to ensure unmatched versatility and durability in the market.
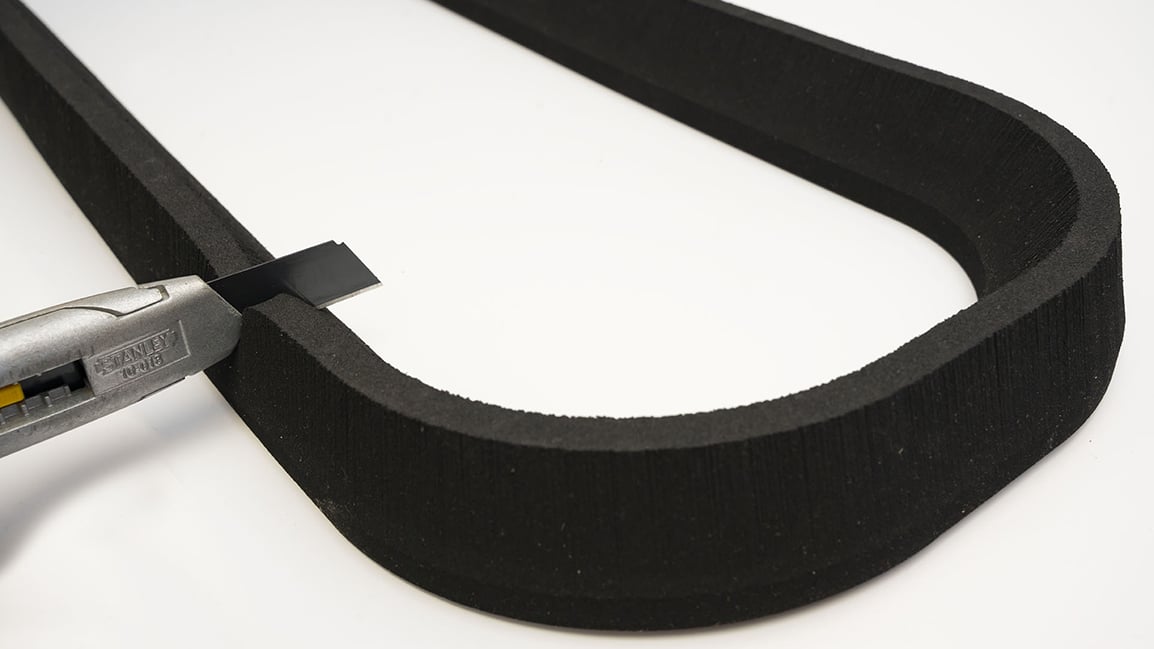
Depression Modes of our bubble leak test equipment
Our different suction box are equipped with a hybrid vacuum system that operates either by venturi effect when coupled with a compressor (1) or by a vacuum pump or vacuum pump box (2).
Regardless of the mode of operation, our vacuum box have a rapid vacuum release system to allow quick detachment and repositioning of the box for successive leak testing.
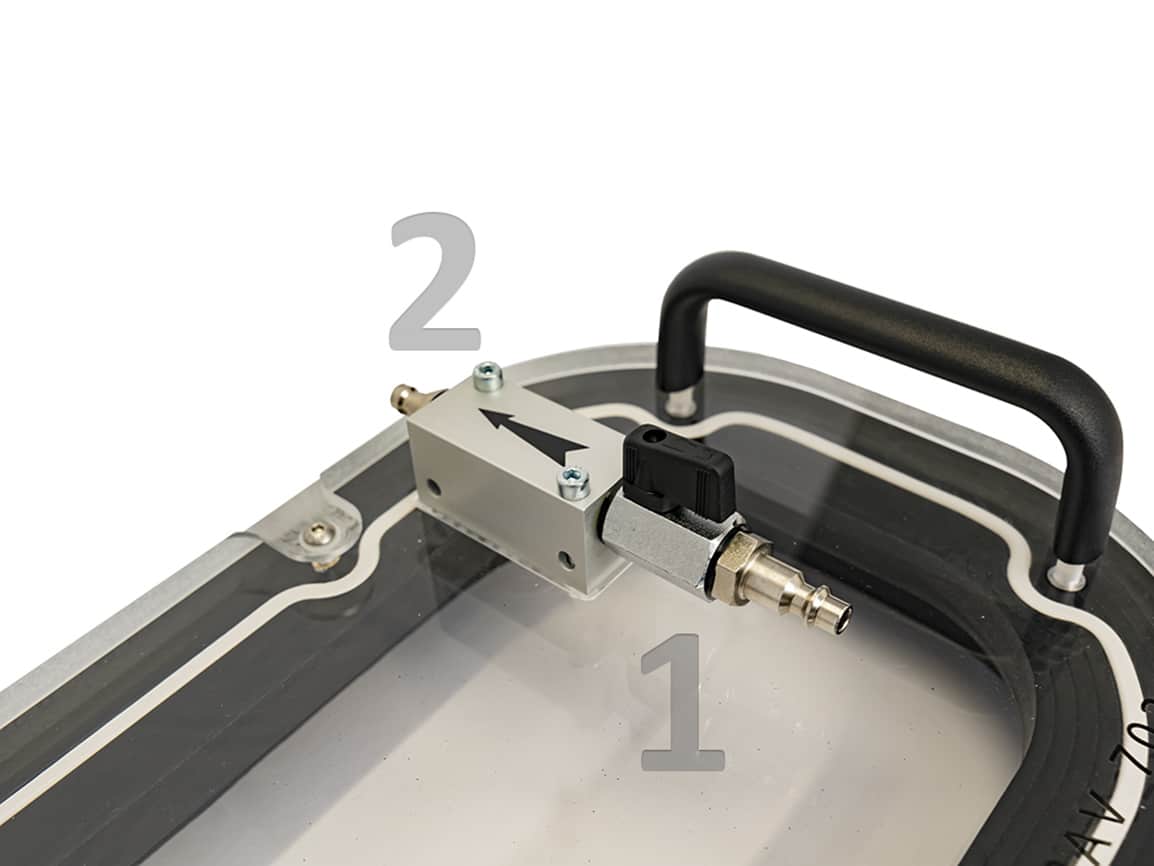
Vacuum Control and Regulation
To verify that the conditions for vacuum leak testing are suitable and thus ensure defect detectability, it is necessary to ensure that the vacuum is below a certain value (depending on the control standard to which you are subject).
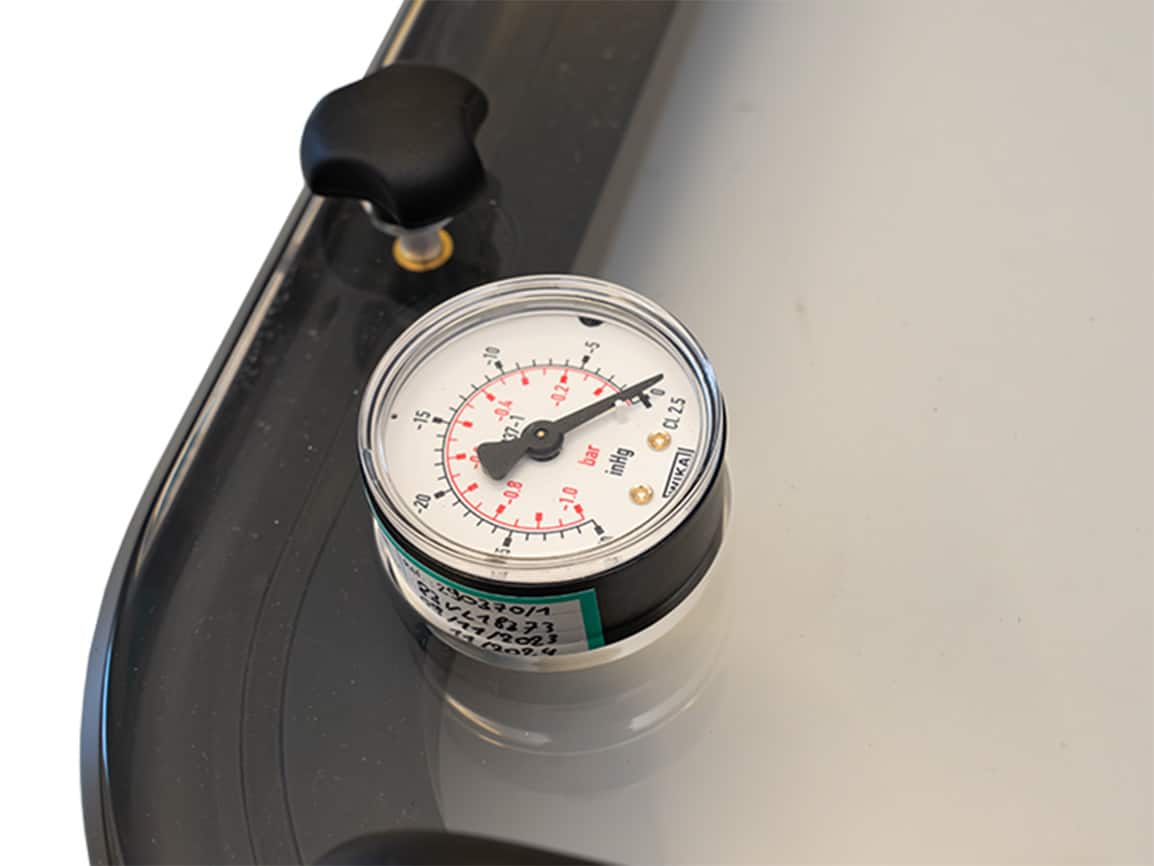
For this purpose, the vacuum box are equipped with a vacuum gauge and a manual regulation system to adjust the maximum vacuum. This adjustment capability will be very useful when testing on thin surfaces where excessive vacuum could deform the surface itself.
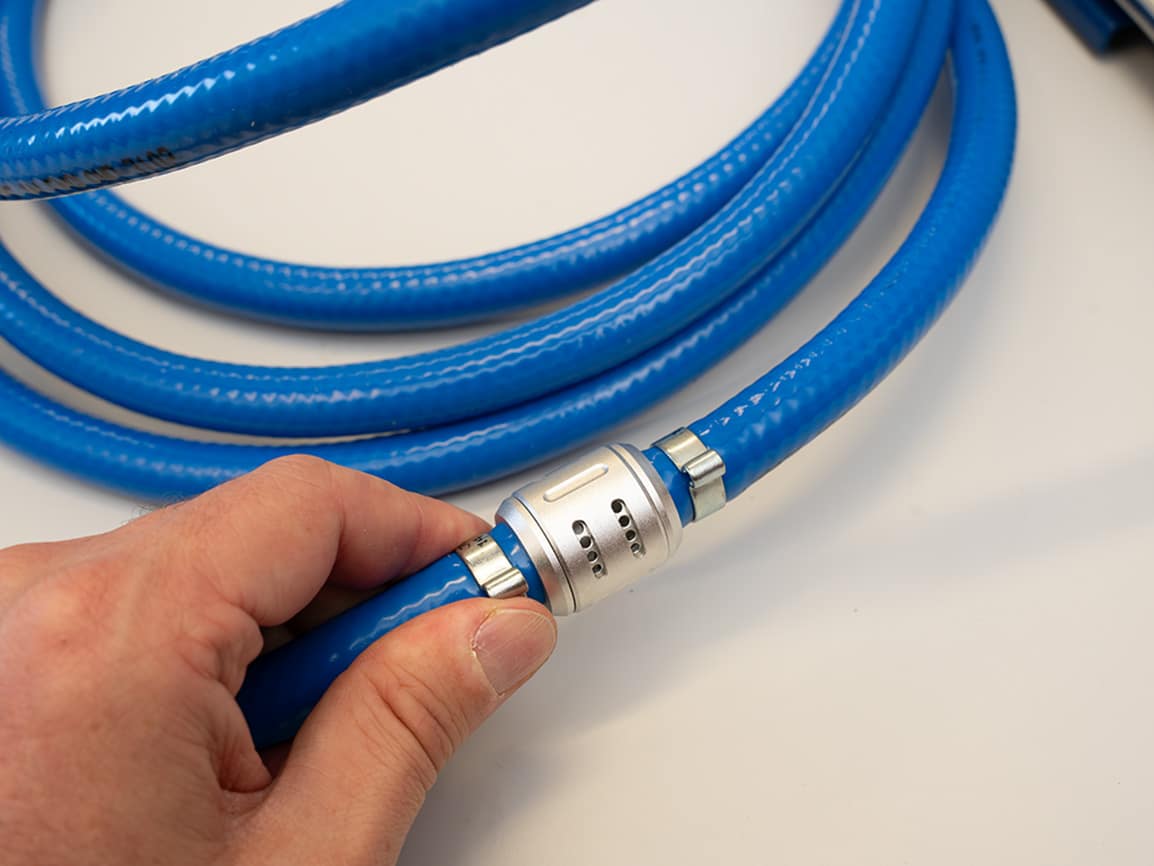
Associated Standards for Leak Testing LT
NF EN 1593 Non-destructive testing – Leak testing – Bubble test
NF EN 1779 Non-destructive testing – Leak testing – Criteria for method and technique selection
NF EN 13184 Non-destructive testing – Leak testing – Pressure change method
API 650 – Vacuum box test pressure procedure
Example of leak testing inspection procedure: API 650 – vacuum box testing tank bottom
Main requirements of the API 650 for vacuum box inspection :
- The temperature of the elements to be inspected must be between 4° and 52°C (39.2° and 125.6°F).
- The soap solution must be applied to the surface being inspected until it is thoroughly wetted.
- The pressure conditions inside the bubble leak test equipment should be between 3 and 5 psi, or 21 to 35 kPa.
- The vacuum must be maintained at this level for at least 5 seconds.
- There must be an overlap of the inspected areas of at least 2 inches or 50mm when the vacuum box weld testing equipment is moved.
- …